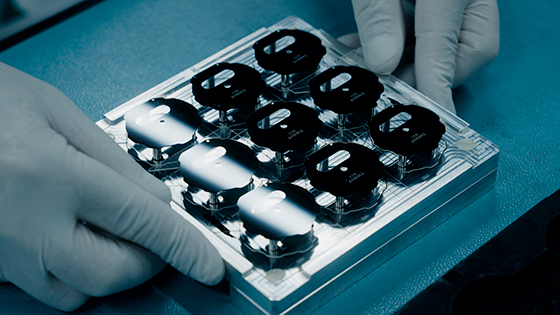
The brand from Le Locle has made a substantial investment in an ultra-sophisticated laboratory dedicated to producing the solar-sensor dials for the T-Touch Connect Sport. A production line covering all four stages of the manufacturing process has been set up. From thin-film coatings to quality control, all operations take place in a clean-room environment.
To develop its solar technology, Tissot has injected some 20 million francs into a cutting-edge lab managed by Nivarox-FAR, a Swatch Group entity. Within a 1,000sqm area, 25 people work daily in several clean rooms on the meticulous design of solar-sensor dials, intended for the time being to equip the brand’s flagship model: the T-touch Connect Sport. This model that remains a veritable time-keeper stems from several years’ development and incorporates new technologies combining solar cells with Swiss watchmaking expertise. In addition to the accuracy of real hands, impressive autonomy and sporty characteristics, this timepiece runs for months on end, keeping time and meeting its owner’s objectives.
Production process
Central to this watch’s innovation is the photovoltaic cell. Crafted using materials like glass, silicon, zinc oxide, aluminium, silver and resins, each solar cell provides energy equivalent to five button batteries annually. Designed and manufactured by Nivarox-FAR – a Swatch Group company – the photovoltaic cells excel in low-light conditions, marking a new benchmark in Swiss watchmaking. This sophisticated design artfully incorporates the PV cell within the watch dial, making semi-transparent decorative dials redundant.
The production of the solar cells for watches begins at the front end of the manufacturing line, where a glass wafer is coated with a stack of thin films consisting of a transparent front contact, a thin film silicon diode and metallic back contact. An incredibly small amount of silicon is used, even less than could be found on a grain of sand. Then the wafer undergoes patterning, a stage involving high-power and ultra-short laser pulses – the peak power is equivalent to that of a high-speed train – which etch the solar cell design into the silicon. A current collection grid and protective layers are added by screen printing. During the back-end phase, techniques such as drilling and laser dicing ensure that the solar cell can withstand shocks of up to 5000G. Finally, every cell is checked visually and electrically for its performance across a range of lighting conditions.
For the AMOLED integration part, EM Microelectronic, another Swatch Group company, provides its expertise and know-how. The process begins with the application of a flexible connection cable to the Solar Cell dial. Bonding the cable with “ACF” subsequently ensures electrical connectivity. In the next step, an AMOLED display is attached to the Solar Cell using a transparent optical resin, which brings multiple benefits as it enhances the display’s contrast, increases mechanical robustness and avoids particle intrusion by eliminating traditional air gaps. Following the fully automated, high-precision optical bonding, a metal support is added as part of preparing the dial for its integration into the final watch. To ensure the highest quality principles, the AMOLED and solar cell module is subjected to stringent piece-by-piece funtional testing. Whilst the display is tested with a multitude of test patterns, the solar cell is characterised in the “Sun Test” for various lighting intensities simulating a range of everyday uses. The process concludes with a final visual inspection by expert watchmaking-level operators, ensuring only truly impeccable dials make it through to final watch assembly.
In today’s era, advancements in solar technology hold paramount importance. As global conversations revolve around sustainability and energy efficiency, innovations like these are not just desirable but important and imperative. The Swatch Group has understood this and is making great strides in this development, which is already taking shape at the heart of the T-Touch Connect Sport, a true benchmark in the field. Other innovative timepieces incorporating this technology are due to be unveiled shortly.
August 29, 2024