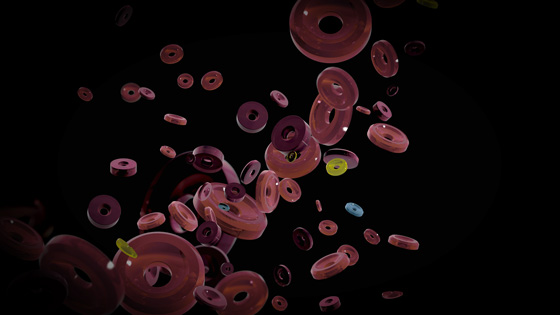
Acquired in 2017 by the Acrotec group, the Gasser-Ravussin and Pierhor companies, both active in the production of synthetic watch jewels, merged one year later and at the same time united their activities under one roof in Ecublens.
Created 15 years ago by François Billig, the Acrotec Group currently comprises 18 companies and employs some 1,200 people. Pursuing the main goal of supplying high-quality Swiss made products to all watch manufacturers and brands, the group is currently one of the most important independent suppliers in the world of Swiss industrial subcontracting. By manufacturing shock absorbers, oscillating weights and complete barrels, Acrotec offers three of the five components representing essential sub-assemblies in a watch movement.
Already the owner of Kif Parechoc, Acrotec was looking to acquire a supplier of synthetic jewels in order to guarantee the supply of its shock absorbers. The opportunity presented itself in 2017 with Gasser-Ravussin, a more than century-old company established in Lucens, in the La Broye region (Canton Vaud). That same year, the group decided to further expand its activities in the field of synthetic watch jewels for the watchmaking and industrial sectors and acquired the firm Pierhor, based in Ecublens. In 2018, the two entities merged under the name Pierhor-Gasser. The employees of Lucens then joined the Ecublens teams in workshops that were duly renovated. Today, the company has some 60 employees.
Creation of watch jewels
Whether natural or synthetic, watch jewels considerably reduce the friction of the various watch movements and escapement components. The history of this component begins around 1700 in London when the Genevan Nicolas Fatio de Duillier had the ingenious idea of using ruby – a natural jewel, pierced like a pivot bearing – in the design of a calibre. This innovation greatly contributed to the renown of English watchmaking during the 18th century. Although expensive, these jewels were used sparingly in the calibres of the time.
In 1902, Auguste Verneuil invented corundum, a synthetic watch jewel obtained by fusing aluminium oxide powder with chromium oxide which gives it a distinctive red colour. This new “jewel” resembled a pear measuring 2 to 3 cm in diameter called a boule and combined all the qualities of natural ruby. The strongest crystal after diamond, synthetic ruby has a hardness of 2,000 Vickers.
Watch jewel production
Pierhor-Gasser manufactures some 30 million watch jewels per year. The manufacture of these models begins on the basis of preparations prepared by two Swiss suppliers specialising in this field. Synthetic watch jewels thus began their long creative journey in the form of small rounded components. This process requires the know-how and experience of each employee, as there are no apprenticeships in this field.
The first step is to laser-drill the centre of the synthetic components. This drilling step then allows an operator to thread one by one the small watch jewels on a wire (threading) in order to make small “necklaces”. These are then sent on to the next workshop where they are inserted in dedicated containers called navettes (shuttles), before being meticulously covered with Wood’s metal, a bismuth, tin and cadmium alloy with a melting point of 71°, enabling better subsequent dilution. The shuttles, containing about a thousand jewels, find their way to a workshop devoted to enlarging the inner hole, the size of which varies according to the orders. This operation consists of a wire lapping process to obtain holes with a diameter ranging from 0.07 to 2.0 millimetres. By means of no less than eight complex operations, the company’s expertise serves to achieve a nanometric surface finish with micron-level tolerances.
Once the inner hole is exactly the size it should be, the Wood’s metal is diluted, freeing the jewel “necklaces” from the shuttle. This operation is called dégommage (degumming). Before proceeding to a new threading step, the watch jewels are scrupulously checked. Once they are assembled on a new wire, “turning” specialists come into play. This phase consists of adjusting the outside diameter of the stone by grinding it with the utmost delicacy. The know-how of the company’s specialists guarantees a precision of ± 2 μm.
The complexity of these components means that they must also be hollowed out in their centre, and sometimes also olive-cut. The workshop dedicated to these delicate operations has dozens of machines that machine the stones one by one to create this recess. This technique makes it possible to guarantee a tolerance of ± 0.050 mm on the diameter of ± 10 μm on the height of the hole. In order to ensure the optimal efficiency of the jewel bearing, it is then olive-cut, depending on the customer’s request. Olive-cutting removes the sharp edges of the inner hole, thus reducing the friction surface of the pivots and facilitating movement lubrication. The technology used makes it possible to achieve tolerances of ± 2 μm for the diameter of the hole, while guaranteeing the desired geometry and surface finish.
Delicately lined up on dedicated in-house supports, the jewels then go through the polishing stage. As with all the previous operations, the specialist’s know-how will set the finishing touch to the quality of these micro-components, which are of crucial importance in the smooth running of a calibre. The choice of brushes – of which the bristles may be natural (vegetable or animal), synthetic or metallic –, as well as the pressure applied to the jewels and the duration of the process are all of prime importance in this phase of the work.
The final operation consists of checking the synthetic watch jewels, either in batches or individually. To do this, Pierhor-Gasser has a complete range of means at its disposal, from Keyence equipment to vertical and horizontal benches fitted with sensors. In addition, the firm is equipped with QuickControl Pro software guaranteeing better traceability and management of the controls carried out throughout the manufacturing process, all of which facilitates final tests.
Certification
Driven by a concern for customer satisfaction and in order to validate its manufacturing processes reaching accuracies of a few microns or even a few nanometres, the company launched an ISO 9001 certification process which was completed at the beginning of this year. This project has also made it possible to unite the staff of the two merged companies around a new common goal.
This first certification was just one step towards an even more ambitious level of requirements, namely ISO 13485 certification, which lays down the rules for a quality management system specific to the medical device sector. The company is currently 80% dedicated to the watchmaking sector, 10% to the fields of waterjet cutting and inkjet printing, and 10% to the medical sector, a division that it would like to strengthen in the future.
Gasser-Ravussin
Born in the historical hub of watch jewel production, the Manufacture was created in Lucens in 1925 by Paul Gasser and his wife née Ravussin. In 1971, the company became part of the Société des Garde-Temps (S.G.T.) which launched the SGTSHOCK shock absorber two years later. In 1980, the Vaud-based Maison regained its independence. At the end of the 20th century, production was achieving record results. The company management took advantage of this to modernise equipment, create new products and significantly improve the quality of the components sold. The Acrotec Group acquired the firm in 2017.
Pierhor
Founded in 1899 by Arthur Sueur in Yverdon, the firm specialising in the manufacture of watch jewels as well as synthetic stones for other industries, named after its founder. Sold to Pierre Colelough in 1960, it was transferred to Chavannes-près-Renens and renamed Pierhor. In 1994, François Durafourg acquired
August 27, 2020