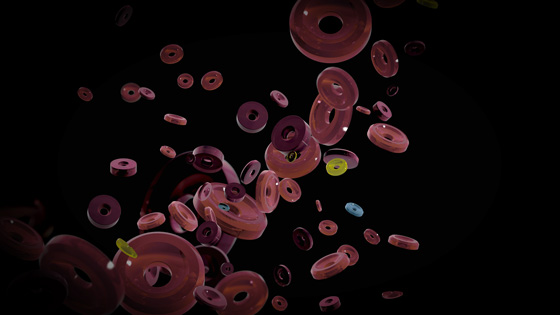
Acquises en 2017 par le groupe Acrotec, les maisons Gasser-Ravussin et Pierhor, toutes deux actives dans la production de pierres synthétiques, fusionnent un an plus tard et réunissent par la même occasion leurs activités sous un même toit à Ecublens.
Créé il y a quinze ans par François Billig, le groupe Acrotec compte à ce jour 18 entreprises et occupe quelque 1’200 employés. Avec pour but principal de fournir des produits Swiss made de haute qualité à l’ensemble des manufactures et marques horlogères, le groupe est aujourd’hui l’un des fournisseurs indépendants les plus importants dans le monde de la sous-traitance industrielle suisse. En fabriquant des antichocs, des masses oscillantes et des barillets complets, Acrotec propose trois des cinq composants, sous-ensembles essentiels dans le mouvement d’une montre.
Déjà propriétaire de Kif Parechoc, Acrotec cherchait à acquérir un fournisseur de pierres synthétiques afin de garantir l’approvisionnement de ses antichocs. L’opportunité s’est présentée au travers de la maison Gasser-Ravussin, entreprise plus que centenaire établie à Lucens, dans la Broye vaudoise. La même année, soit en 2017, le groupe décide d’élargir encore ses activités dans le domaine des pierres synthétiques destinées à l’horlogerie et à l’industrie et acquiert la firme Pierhor, établie à Ecublens. En 2018, les deux entités fusionnent sous le nom de Pierhor-Gasser. Les employés de Lucens rejoignent alors les équipes d’Ecublens au sein d’ateliers qui seront rénovés. Aujourd’hui, l’entreprise compte quelque 60 collaborateurs.
Création des pierres d’horlogerie
Naturelles ou synthétiques, les pierres d’horlogerie diminuent considérablement les frottements des différents mobiles de la montre et des organes de l’échappement. L’histoire de ce composant commence vers 1700 à Londres alors que le Genevois Nicolas Fatio de Duillier a l’ingénieuse idée d’utiliser le rubis, pierre naturelle, percé comme un coussinet de pivotement dans la conception d’un calibre. Cette innovation contribuera grandement à la renommée de l’horlogerie anglaise au cours du 18e siècle. Onéreuses, ces pierres étaient toutefois utilisées avec parcimonie dans les calibres de l’époque.
En 1902, Auguste Verneuil invente le corindon, pierre synthétique obtenue par fusion de poudre d’oxyde d’aluminium avec de l’oxyde de chrome qui lui donne sa teinte rouge. Cette nouvelle «pierre» se présente sous l’aspect d’une poire de 2 à 3 cm de diamètre appelée boule et qui réunit toutes les qualités du rubis naturel. Cristal le plus solide après le diamant, le rubis synthétique présente une dureté de 2’000 Vickers.
Fabrication des pierres
Pierhor-Gasser usine quelque 30 millions de pierres d’horlogerie par année. La fabrication de ces pièces débute sur la base de préparages élaborés par deux fournisseurs suisses spécialisés en la matière. Et c’est donc sous la forme de petites pièces arrondies (rondelles) que les pierres synthétiques commencent leur long parcours de création. Ce processus nécessite le savoir-faire et l’expérience de chaque employé, aucun apprentissage n’existant dans ce domaine.
La première des étapes consiste à percer les pièces synthétiques par laser en leur centre. Cette étape, appelée perçage, permet ensuite à une opératrice d’enfiler une à une les petites pierres sur un fil (enfilage) afin d’en faire de petits «colliers» de pierres. Ces derniers passent alors dans l’atelier suivant où ils sont insérés dans des navettes, puis minutieusement recouverts de métal de Wood, alliage de bismuth, d’étain et de cadmium, dont le point de fusion est de 71°, ce qui permet de mieux le diluer ultérieurement. Les navettes, renfermant quelque mille pierres, prennent le chemin d’un atelier dédié au grandissage du trou intérieur dont la grandeur varie en fonction des commandes. Cette opération consiste en un processus de rodage sur fil permettant la création de trous d’un diamètre allant de 0,07 à 2,0 millimètres. Le savoir-faire de la maison permet d’obtenir un état de surface nanométrique et d’atteindre une tolérance de quelques microns. Pour arriver à ce résultat pas moins de huit opérations complexes sont nécessaires.
Lorsque la précision du trou intérieur est obtenue, le métal de Wood est dilué, libérant ainsi les «colliers» de pierres de la navette. Cette opération porte le nom de dégommage. Avant de procéder à une nouvelle étape d’enfilage, les pierres sont scrupuleusement contrôlées. Ainsi rassemblées sur un nouveau fil, les spécialistes du «tournage» peuvent opérer. Cette phase consiste à ajuster le diamètre extérieur de la pierre en la meulant avec la plus grande délicatesse. Le savoir-faire des spécialistes de la maison garantit une précision de ± 2 μm.
La complexité de ces pièces veut qu’elles soient encore creusées en leur centre, voire olivées. L’atelier dédié à ces délicates opérations dénombres des dizaines de machines qui usinent, une à une, les pierres pour leur conférer une creusure. Cette technique de travail permet de garantir une tolérance de ± 0,050 mm sur le diamètre de ± 10 μm sur la hauteur du trou. Afin d’apporter une efficacité optimale à la pierre, elle est ensuite, selon les demandes, olivée. L’olivage supprime les arêtes vives du trou intérieur, diminuant ainsi la surface de frottement des pivots et facilitant la lubrification du mouvement. La technologie utilisée permet d’atteindre des tolérances de ± 2 μm pour le diamètre du trou, tout en garantissant la géométrie et l’état de surface souhaités.
Délicatement alignées sur des posages maison, les pierres passent ensuite par l’étape du polissage. Comme pour toutes les opérations précédentes, le savoir-faire du spécialiste parachèvera la qualité de ces micros pièces qui ont une importance cruciale dans le fonctionnement d’un calibre. Choix des brosses - dont le poil peut être en soies naturelles (végétale ou animale), synthétiques ou métalliques - pression opérée sur les pierres et durée du processus sont primordiaux dans cette phase de travail.
L’ultime opération consiste à contrôler, par lots ou pièce par pièce, les pierres synthétiques. Pour ce faire, la maison Pierhor-Gasser dispose d’une palette complète de moyens allant des appareils Keyence, aux bancs verticaux et horizontaux avec capteurs. De plus, la firme est équipée d’un logiciel QuickControl Pro garantissant une meilleure traçabilité et gestion des contrôles réalisés tout au long du parcours de fabrication ce qui facilite les tests finaux.
Certification
Soucieuse de la satisfaction de ses clients et afin de valider ses procédés de fabrication atteignant des précisions de quelques microns, voire de quelques nanomètres, l’entreprise a lancé un processus de certificat ISO 9001 qui a abouti au début de cette année. Ce projet a également permis de fédérer le personnel des deux sociétés fusionnées autour d’un nouvel objectif commun.
Cette première certification n’est qu’une étape vers un niveau d’exigences encore plus ambitieux, à savoir la certification ISO 13485 qui établit les règles relatives à un système de management de la qualité propre au secteur des dispositifs médicaux. L’entreprise se dévoue actuellement à 80% pour l’horlogerie, 10% pour les domaines de la découpe jet d’eau et de l’impression jet d’encre et 10% pour le secteur médical, division qu’elle aimerait justement renforcer à l’avenir.
Gasser-Ravussin
Née dans le berceau de la fabrication des pierres d’horlogerie, la manufacture a été créée à Lucens en 1925 par Paul Gasser et son épouse née Ravussin. En 1971, l’entreprise intégrera la Société des Garde-Temps (S.G.T.) qui lancera, deux ans plus tard, l’amortisseur de chocs SGTSHOCK. La maison vaudoise redeviendra indépendante en 1980. A la fin du vingtième siècle, la production vole de records en records. Les dirigeants en profitent pour moderniser les équipements, créer de nouveaux produits et améliorer notablement la qualité des pièces vendues. Le groupe Acrotec acquit l’entreprise en 2017.
Pierhor
Fondée en 1899 par Arthur Sueur à Yverdon, la firme, spécialisée dans la fabrication de rubis d’horlogerie et de pierres synthétiques pour l’industrie, prend le nom de son fondateur. Vendue à Pierre Colelough en 1960, elle est transférée à Chavannes-près-Rennens et porte alors le nom de Pierhor. En 1994, François Durafourg acquiert l’entreprise et la transfère à Ecublens. Il reste à sa tête jusqu’au rachat, en 2017, par le groupe Acrotec.
27.8.2020