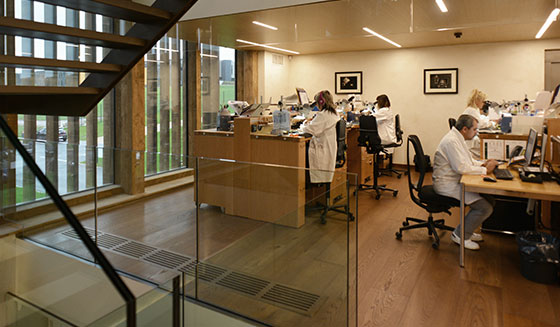
Adjoining the manufacturing facility in La Chaux-de-Fonds, the House of Arts and Crafts brings together the most precious craft activities applied to watchmaking. Some of them have even been revived here.
Previously based in the manufacture at Le Crêt-du-Locle, the entity uniting the arts and crafts activities has now moved to an old farm built in the Bernese style, dating from the late 18th century and adjoining the main building. Its own architecture makes the new House of Arts and Crafts the impressive symbol of a successful encounter between tradition and modernity. While the spirit of the place remains intact, the internal structure has been entirely redesigned and an unseen network of high technology installed. The creation of the House of Arts and Crafts is a pioneering gesture by which Cartier has taken up the challenge of sublimating tradition and anchoring these expert skills in modernity.
On the ground floor
The 350 m2 on the ground floor surround the entrance hall and lead on to the Big Salon, the Small Salon and the presentations room. The allocation of space on this floor testifies to Cartier’s determination to lay these craft activities open to sharing and exchange: meetings with craftsmen and visits to the workshops.
When a visitor enters the Big Salon, he or she is immediately immersed in the spirit of olden times. The wood panelled walls and floors - using pine wood reclaimed from other surrounding farms - create a warm atmosphere. The central fireplace evokes the cold evenings of yesteryear when the whole family was grouped around this comforting hearth. The windows are subdued light wells opening onto green outdoor spaces. While time seems to have stood still here, a big Neuchâtel-style clock reminds visitors that time is moving on and that they are indeed living in the 21st century.
On the first floor
This first floor is home to the traditional crafts such as gemstone setting, jewellery and polishing. Part of this space is dedicated to Cartier’s foremost profession, jewellery. And jewellery naturally involves gemstone setting. All the different techniques are applied here, i.e. claw setting, sunken setting, grain setting, closed setting etc. Polishing also plays a key role because the brilliance and éclat of a piece depend on it, as too does the wearer comfort. Extremely technical, it requires years of experience and must be performed with mastery and patience.
While traditional techniques occupy a prominent position they do nevertheless leave room for forgotten skills. Often handed down from one craftsman to the next, these ancient crafts have lapsed into oblivion with the passage of time. Cartier has set itself the task of surveying, understanding and updating these treasures of craftsmanship. In that spirit, it has brought two techniques that had disappeared up to date again: granulation and filigree work.
Granulation made its appearance in the third millennium BC. However, its expression reached its height in the eighth century BC with Etruscan art. With a profusion of gold grains, the technique of granulation consists in producing small spheres from pieces of gold wire which are first cut, then rolled in charcoal dust and heated on an open flame. The grains are then assembled one by one and fuse with the gold sheet to create the motif in relief. In 2013, Cartier created a watch with granulation in the shape of a panther. Close on 3,800 gold spheres go to make up this work. They are secured to the dial in groups of five. Almost 3,500 separate baking operations were necessary for its production. Forty hours were devoted to the engraving of the motif and nearly 320 hours to putting the spheres in place. This artistic masterpiece has been made in a series of just twenty pieces.
The Sumerians are believed to have invented filigree work. The earliest objects created by this art originating from Troy and Ur have been dated to 3000 BC. The craftsmen had to adapt this technique to the criteria of the house and the scale of the watchmaking universe. Nowadays, the gold or platinum wire is twisted before being hammered flat. Then it is modelled to form the motif and soldered in position. In 2015, Cartier reinvented this technique and associated it with lacquer work and gemstone setting. The Ronde Louis Cartier model, with a panther décor, displays these techniques; the filigree work alone required ten days to complete. This model too has been made in an edition of just twenty pieces.
On the second floor
The techniques of marquetry, mosaic and enamelling share this floor. These ancestral techniques which emerged at a very early stage in history, marquetry - in wood or straw - and stone mosaics are applied today to the miniature scale of Cartier watch dials. The material is chosen for its colour, texture and individual character. Carved in minute elements which go to make up the motif, these fragments are hand-assembled by a process which requires meticulous workmanship.
In 2014, an all-new technique in watchmaking was added to the house repertoire: floral marquetry. For this rare and delicate activity, the craftsmen perform a series of particularly detailed operations: gathering the real petals, colouring and cutting out each petal, placed on a thin piece of wood using a marquetry «crossbow» saw. Once assembled, these elements reveal the full design. This is exacting work in which each phase plays a vital role: a clumsy gesture and the craftsman must go back to square one. This prowess requires immense concentration and two weeks of hard work dedicated entirely to marquetry. Another three weeks are then needed to make the dial of the Ballon Bleu floral marquetry watch, with a parrot decor.
Two complementary mosaic techniques are used by Cartier: miniature squares applied to the dial background and tessera with irregular shapes to make up the pattern. The composition is rigorous and the colours vary according to the nature of the gemstones. Last year, Cartier created a dial with a stone mosaic representing a tiger. This spectacular piece incorporates nearly 500 minute tessera; between 30 and 40 hours of work were needed for the background and 25 to 30 for the decor.
What would the craft trades be without enamel? Champlevé enamel, plique-à-jour enamel, grisaille enamel, painted enamel or gold paste grisaille enamel… The latter of these techniques consists in covering a sheet of gold with a uniform layer of black enamel. The craftsman then uses a needle or ultra-fine brush to apply a gold paste which he works to create effects of depth and relief. Next the dial is baked in an oven. Made in 80 pieces in 2014, the Rotonde watch with a panther décor is a superb example of this process.
Walking round the House of arts and crafts, the visitor finds himself carried away to another world, a world of magic and dreams in which the craftsmen vie with one another to find ingenious solutions recreating forgotten skills, perfecting those which still exist or quite simply innovating!
April 02, 2015