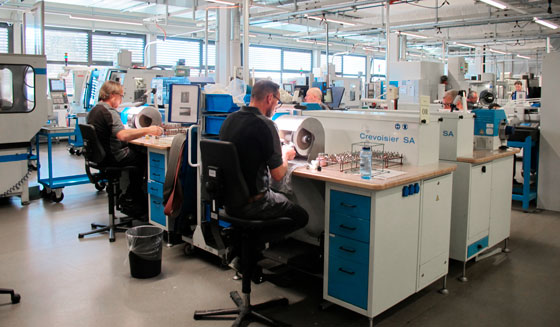
Stemming from a wish to bring case and dial production together in the same location, Les Ateliers d’Hermès Horloger offer brands a unified, high-performance and responsive service aimed at achieving excellence and guaranteeing confidentiality.
It all began back in 1912 when Emile Hermès asked his saddle and leather-making artisans to create a leather strap to protect his daughter Jacqueline’s pocket watch. At the end of the 1920s, the historical Hermès boutique at 24 Faubourg Saint-Honoré in Paris began selling watches. Fifty years later, in 1978, the Maison set up its watchmaking subsidiary in Brügg, a village on the outskirts of Biel/Bienne. Along this more than century-long watchmaking path, the brand has secured the precious services of various suppliers while investing in their companies or simply buying them up.
The year 2006 saw a major breakthrough for Hermès in its approach to suppliers. After setting up an atelier specially dedicated to crafting leather straps, the Maison acquired a stake in the movement-making company Vaucher Manufacture Fleurier. It entirely bought up the dial-maker Natéber SA in 2012 and also purchased shares in the case-making company Joseph Erard SA, before taking it over entirely in 2013.
The dial
If the movement is the soul of a watch, the dial is its expression and one of the key elements in its aesthetic appeal, as Natéber has been committed to demonstrating since 1972.
From the basic material to the finished article, no less than 20 operations are involved in making a so-called “simple” dial, and up to 60 for a “complex” one. In the workshop of a dial-making artisan, industrial considerations are not always paramount: each new model requires the implementation of innovative technical solutions. This approach calls for considerable versatility and flexibility on the part of staff members.
A dial-maker is a jack of all trades, a kind of alchemist who must know the properties and secrets of a wide variety of materials such as brass, gold, aluminium, carbon fibre, mother-of-pearl and sometimes enamel and precious stones.
Making a dial begins in the mechanical workshop, which develops the necessary tools, including dedicated swages and bases. It ends with the one dedicated to the assembly of the many components. Each dial makes a lengthy journey between the first and last step, not to mention a considerable amount of back-and-forth transitions and many different testing protocols. It passes through at least seven other workshops for processes such as polishing, decoration, electroplating, varnishing and lacquering, transfer printing and sometimes gemsetting.
The case
An essential part of a watch exterior, a case must be functional, durable and robust. The Joseph Erard family firm based in Le Noirmont has made this a speciality.
Producing a case is first and foremost the art of working with noble metals: steel, gold and titanium, and sometimes rarer materials such as platinum and palladium. Then comes the turn of engineers to transform ideas into manufacturing plans. And finally, the process naturally involves mastering production as such, which may take different paths depending on the objects: machining or stamping.
Finally, the various case components thus produced must be finished before being fitted with the watch ‘engine’ (movement). A number of treatments await them, including polishing, welding and assembly, along with final controls and water-resistance testing.
Les Ateliers d’Hermès Horloger
In 2009, Joseph Erard set up in a brand-new 2,000 sqm building located in the industrial zone of Le Noirmont. Natéber transferred its activities to this site at the end of 2016, thereby giving rise to Les Ateliers d’Hermès Horloger.
For the past two years, Operations Director Richard Delacrétaz, along with Technical and Quality Director Frédéric Jenny, have been directing their efforts towards the development and production of these two essential watch components – case and dial – in order to achieve a maximum degree of rationalisation. The goal is to produce an entire Hermès watch within ten days. Even though assembly (T2) is done in the watchmaking workshops in Brügg, Richard Delacrétaz is firmly committed to this ambitious objective and is striving hard towards reaching this goal.
With this in mind, the stages involved in the development of dials and cases have been carefully examined and organised into lines or islands, a procedure enabling considerable time-savings. But the entire process begins in the Watchmaking technical department where a dozen or so engineers work on developing and industrialising products, from prototype to series production. Files contained detailed plans, production processes, as well as the tools and machinery required for production are all defined in this department. This approach serves to ensure the production of reliable and robust high-quality components, while maintaining the rules of confidentiality upheld by the company.
Component production also involves the toolmaking workshop, where four specialised mechanics work on creating the tools required for production, especially the swage presses serving to create the shapes required by designers. This key area is extremely responsive, thus enabling considerable time savings.
Equipped with a high-performance machinery fleet – including for five-axis machining, preparation for polishing and washing –, all the workshops operate according to the 5S method, thereby ensuring a functional and clean working area that contributes to enhancing productivity and quality. The dial production process includes an electroplating area with 24 dipping tanks, linked to an ultra-modern wastewater treatment plant.
Creating dials involves blanking, welding, surface treatments such as sunburst brushing, satin finishing and sanding, varnishing-lacquering and cellulose varnishing, transfer printing and in some instances gemsetting; while cases call for stamping, machining, surface preparation, polishing and assembly. Les Ateliers d’Hermès Horloger master all stages in the production of these two key watch components. The facility is also equipped for the assembly of timepieces, performed under laminar flow hoods.
Ecology
Located in the rural setting of Le Noirmont, this site is designed to reduce the environmental impact of production measured in terms of its carbon footprint. While the building is currently heated by heat pumps, this system will be replaced by wood heating as of next winter via a central district heating system. Two water-treatment plants handle the wastewater from the factory, especially that resulting from electroplating. Like the Maison Hermès itself, the watchmaking workshops are certified by the RJC (Responsible Jewellery Council).
Richly endowed with ultra-modern production facilities and age-old expertise, Les Ateliers d’Hermès Horloger naturally serve the Hermès brand, but also offer their services to other watch firms. Confidentiality and discretion remain the watchwords of the Maison.
May 24, 2018