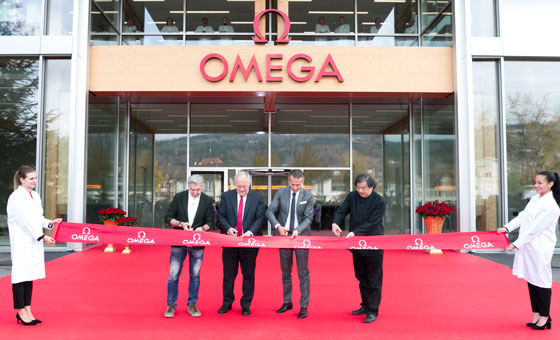
Destiné à accueillir les processus d’assemblage, de tests et de contrôles qualité des montres, un nouveau bâtiment avant-gardiste, fruit de l’imagination du célèbre architecte japonais Shigeru Ban, a été inauguré par la maison biennoise début novembre.
Une centaine de journalistes et autorités locales et cantonales ont découvert, le 2 novembre dernier, le nouvel outil de production d’Omega. Avec l’ouverture de cette manufacture futuriste, la marque écrit un nouveau chapitre de son histoire. C’est en effet en 1882 que l’entreprise Louis Brandt & Fils a déplacé son site de production au 96 de la rue Jakob-Stämpfli à Bienne. Connue aujourd’hui sous le nom d’Omega, la maison a toujours gardé le même emplacement. Elle n’a toutefois pas cessé de croître. Le fleuron inauguré est certainement la plus importante de toutes les extensions réalisées.
Juxtaposant les bâtiments historiques de la marque, la nouvelle manufacture, s’étirant sur cinq étages, est un vrai chef-d’œuvre de développement durable, entièrement faite de bois d’épicéa suisse, de béton et de verre, agencés de façon admirablement optimisée. Innovation technique et expertise humaine cohabitent en parfaite harmonie pour fluidifier au maximum le processus de fabrication des garde-temps. Omega en tire un avantage clé: l’efficacité. Ce nouveau bâtiment réunit sous le même toit chacune des étapes de fabrication, de l’assemblage des montres (T2) à leur emballage (T4), en passant par le montage des bracelets (T3), ainsi qu’un espace de stockage et toutes les fonctions logistiques. De plus, grâce à une conception facilitant l’apprentissage, il permet à la maison d’affiner et d’améliorer constamment les compétences de ses collaborateurs.
Le génie de Shigeru Ban
A l’origine de ce bijou de technologie et de logistique, l’architecte japonais Shigeru Ban, célèbre pour ses structures sophistiquées et son goût pour les techniques non conventionnelles. Musées tout en courbes en France ou église en carton au Japon, il est également le concepteur du Centre Nicolas G. Hayek de Tokyo.
En associant des thèmes issus de l’architecture japonaise et du modernisme occidental, Ban a créé un style personnel unique. Il est également reconnu pour ses travaux ingénieux à partir de matériaux inattendus, comme les tubes en papier et en carton, qui ont ouvert la voie à des structures recyclables à bas coût. Mais il maîtrise également, et de manière spectaculaire, l’utilisation du bois et du verre, qui composent plusieurs de ses réalisations aux quatre coins du monde, dont notamment le siège d’Omega à Bienne.
Un écrin de technologie
Ce nouvel outil de production est autant impressionnant de l’extérieur que de l’intérieur. Cette structure de 70 mètres de long pour 30 mètres de large sur 30 mètres de haut, marie savamment divers matériaux.
A l’avant-garde du développement durable, cet ambitieux projet présente un ingénieux concept articulé autour de la climatisation et de la consommation d’énergie. Le rendement énergétique a été optimisé au maximum.
Tout d’abord, les techniques d’isolation choisies vont bien au-delà des contraintes imposées par le code de la construction suisse, permettant ainsi de réduire la consommation électrique du système de chauffage du bâtiment. Sur l’extérieur vitré, des pare-soleil équipent chaque fenêtre et s’ajustent à la trajectoire du soleil. L’éclairage intérieur est assuré par des ampoules LED s’adaptant à la lumière du jour et détectant les mouvements afin de s’allumer qu’en cas de nécessité.
L’intégralité de la fourniture en énergie du bâtiment est assurée par un système géothermique qui utilise une source d’énergie renouvelable: les eaux souterraines, pompées via plusieurs puits sur le site.
Pour produire une partie de l’électricité nécessaire au chauffage, au refroidissement, à la ventilation et à l’éclairage renouvelable, le côté sud-est du toit du bâtiment est recouvert de modules photovoltaïques. Les micro-onduleurs développés tout récemment par Belenos (entreprise du Swatch Group) ont été utilisés en première mondiale pour ce bâtiment. Ces éléments sont installés derrière les panneaux solaires. Ils sont directement connectés au réseau électrique, pour lequel ils convertissent le courant solaire direct en courant alternatif renouvelable utilisé dans le bâtiment.
Système de stockage automatisé
Au cœur du bâtiment, Omega a installé un système de stockage entièrement automatisé qui s’étire sur trois étages et 30 mètres de long. Quelque 30’000 caisses renferment tous les composants nécessaires au montage des garde-temps. Deux ascenseurs verticaux véhiculent les boîtes à une vitesse de 4 mètres par seconde et avec une cadence de 1’400 opérations à l’heure. Invulnérable au feu, cet espace renferme un niveau d’oxygène abaissé à 15,2% - normalement 20% -, réduisant ainsi au maximum les risques d’incendie. Seules deux personnes spécialement formées et attestant d’une bonne santé sont autorisées à pénétrer à l’intérieur de ce stock.
Robotisation
La manufacture accueille de nombreux autres exemples de technologie de pointe, comme les bras et systèmes robotisés utilisés entre autres pour les tests Master Chronometer. Pour les humains, le transport et la préparation des montres sont des tâches monotones et chronophages. C’est pourquoi de grands bras robotisés ont été entièrement programmés pour s’en charger. En mesurant, photographiant, remontant, déplaçant et retournant les montres, ils offrent un niveau de production constant et homogène.
D’autres bras robotisés sont utilisés pour l’identification et le conditionnement final des garde-temps. Des systèmes de lecture s’assurent que chaque montre issue de la ligne de montage est livrée avec la garantie et le certificat qui lui correspondent, ainsi que toutes les autres pièces et documents nécessaires. Autre exemple de technologie: les bras utilisés pour la gravure au laser qui donne à chaque montre une identité unique.
Les artisans
Si la robotique se charge des tâches répétitives et ingrates, la place d’honneur est réservée aux artisans, dont le savoir-faire contribue grandement à la qualité des garde-temps de la maison. Régler parfaitement les aiguilles d’un cadran, emboîter soigneusement une montre finie, analyser des résultats de tests ou encore s’assurer que toutes les pièces sont parfaitement réglées… rien ne remplacera l’indispensable main de l’homme.
Les artisans sont incontestablement le plus grand atout de la maison. Pour les aider dans leur tâche, Omega a créé des conditions de travail exceptionnelles au sein de sa nouvelle manufacture. Contrôle précis des températures, climatisation de l’air et ergonomie des stations de travail, tout a été pensé pour plus de fluidité et de confort.
Le nouveau site de tests de METAS
La nouvelle manufacture a été conçue pour accueillir les processus de contrôle qualité et technique de la maison, dont les tests METAS pour la certification Master Chronometer. Tous les équipements nécessaires aux huit tests exigés se trouvent au troisième étage, y compris les puissants aimants qui soumettent la montre à un champ magnétique de 15’000 gauss. Les visiteurs ont même le privilège de bénéficier d’un banc de test leur démontrant l’efficace résistance des garde-temps certifiés Master Chronometer aux champs magnétiques élevés.
Avec ce nouvel outil de production, Omega ouvre non seulement un nouveau chapitre de son histoire, mais entend répondre aux hautes exigences des normes horlogères les plus élevées.
23.11.2017